Lathe tool solutions: efficient processing, precise cutting
Whether it is metal turning, precision parts processing, or mass production tasks, the choice of Cutting Insert for Turning and Lathe tool directly determines the processing efficiency and finished product quality.
We provide the world’s leading Turning Tool Insert and matching tool holders, covering the processing needs of various materials such as stainless steel, alloy steel, cast iron, titanium alloy, etc., to help you easily cope with complex working conditions!
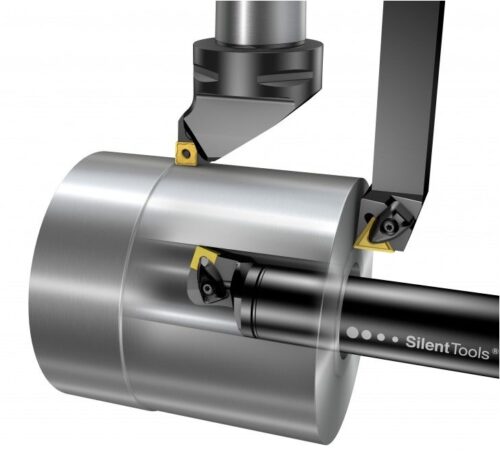
Turning tool product recommendation: Carbide insert + high-rigidity toolholder combination
1. CNMG 120408 negative rake angle insert
Applicable scenarios: Roughing and semi-finishing of stainless steel and high-temperature alloys.
Core advantages: The 8-edge design significantly reduces the cost of a single edge, and with the wear-resistant coating, so,the life is increased by more than 30%.
Recommended toolholder: SCLCR 2525M12, the high-rigidity structure ensures heavy-duty cutting stability.
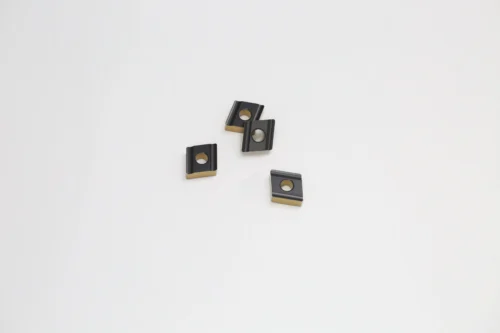
2. WNMG 080408 multifunctional insert
Applicable materials: cast iron, carbon steel and non-metallic composite materials.
Performance highlights: 6-edge economical design, with chip breaker technology, compatible with intermittent cutting and continuous processing.
Applicable toolholder: DSRNR 2525M12, suitable for external cylindrical, end face and profile turning.

3. VBMT 160404 finishing insert
Precision field: high-finish finish turning of titanium alloy and aluminum alloy.
Technological breakthrough: Ultra-fine-grained carbide substrate, combined with TiAlN coating, surface roughness can reach Ra0.4μm.
Tool bar solution: SVJBL 2525M16, negative rake angle design reduces vibration and increases tool life.

Why choose our Turning Tool Insert?
Extreme durability: Using CVD/PVD composite coating technology, the anti-breakage ability is increased by 50%, and the performance is stable under extreme temperatures.
Multi-scenario adaptation: From heavy-duty rough turning to micron-level finishing
So, the full range of insert specifications covers ISO standards and customized requirements.
Cost optimization: Through the upgrade of the number of cutting edges and the design of quick tool change, but,the processing cost of a single piece is reduced by up to 40%.
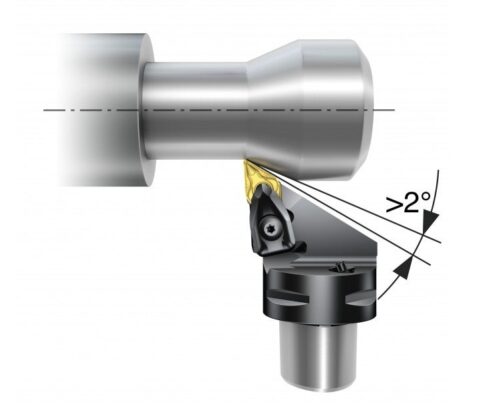
Our Carbide Turning Inserts are widely used in automotive manufacturing, aerospace, mold processing and other fields, but and are recognized by the industry for their excellent cutting performance.
Whether you need a general-purpose insert or a customized solution, our team of engineers will accurately match the tool system for you.