As a manufacturer of cemented carbide tools and had carbide end mill speeds, we know that the correct selection of milling parameters is decisive for machining efficiency, tool life and workpiece quality.
This text will focus on the core parameters of carbide end mill speeds and feeds, especially the setting logic of cutting speed for milling, and attach a practical aluminum milling speed chart. Help you easily meet the challenges of aluminum alloy processing.
Carbide cutting tools with their high hardness, wear resistance and thermal stability have become the tool of choice for high-speed milling. However, if the speed and feed rate are not properly matched, the performance advantage will be greatly reduced. Here are the key steps for parameter setting:

First, the advantages of carbide end milling cutter and parameter setting logic
1.Cutting speed (SFM) :
- the cornerstone of processing efficiency
The cutting speed (Surface Feet per Minute, SFM) directly reflects the relative speed of the tool when it comes into contact with the material. For carbide end mills, we recommend the following general formula:
SFM= Recommended value of tool material × material correction factor
For example, when processing aluminum alloys, the SFM of cemented carbide tools is usually set to 800-2000 SFM (the specific value needs to be adjusted according to the alloy type).
Conversion of speed (RPM) and feed rate (IPM)
Calculation of spindle speed (RPM) according to SFM:
RPM=SFM×3.82/ Tool diameter (in.)
IPM=RPM×FPT×N
Puwei processing aluminum alloy two edge flat end mill parameters recommended:
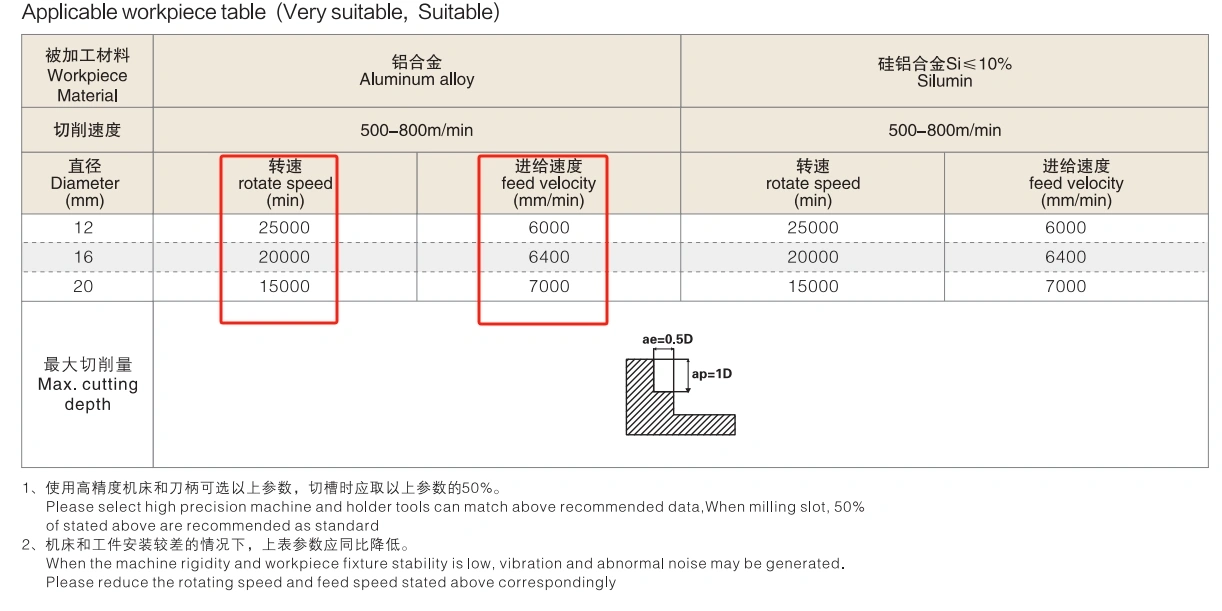
Second, aluminum milling speed meter: accurately match different aluminum alloy types
Because the soft and strong viscosity of aluminum alloy easily causes debris, we need to use high SFM and reasonable feed to improve the surface finish. The following is the recommended parameter range for common aluminum alloys.
Aluminum alloy grade | SFM range is recommended | Feed per tooth (FPT) | Additional advice |
6061-T6 | 1000–1500 | 0.003–0.008 inch | Use a sharp edge to avoid sticking the knife |
7075-T6 | 800–1200 | 0.002–0.006 inch | Preferred coating tool |
5052 | 1200–1800 | 0.004–0.010 inch | Coolant or air cooling is necessary |
In SUMMARY:Let metrics be your efficiency lever
Setting carbide end mill speeds and feeds correctly can not only extend tool life, but also significantly reduce the cost per piece. This aluminum milling speed chart and formula enable you to quickly match aluminum alloy grades to processing requirements. If you need customized parametric solutions or tool selection support, please contact our technical team. We will provide scientific support for every process.