best insert radius for finishing milling steel
When turning finishing, there’s no absolute best inserts radius value as it varies by material. Similarly, for Fine milling of steel and Finish-machining of steel by milling, the choice of milling cutter’s radius also depends on multiple factors.
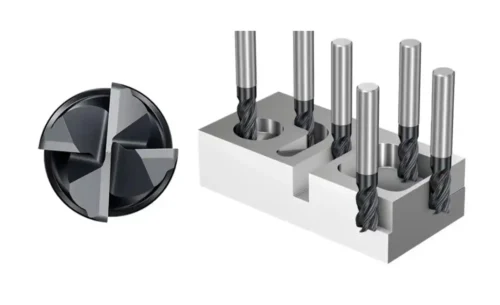
Processing steel parts:
Steel parts are generally medium carbon steel and low carbon steel. The radius of the turning blade is usually 0.4-1.2mm, which is more suitable for steel parts with lower hardness. A smaller finishing blade radius can be selected, which is usually 0.4-0.8mm.
Processing of non-ferrous metals:
For non-ferrous metals such as copper and aluminum, the material is relatively soft, and the blade radius is generally selected to be around 0.2-0.8mm. For example, when finishing aluminum alloys, a blade tip radius of 0.4-0.8mm is more commonly used.
Difficult-to-process materials:
For difficult-to-process materials such as titanium alloy, due to the large cutting force, high cutting temperature and easy wear of the blade, it is necessary to select the optimal blade radius according to the processing conditions, such as 0.8-1.2mm, to improve the blade’s heat resistance and wear resistance.

best insert radius for finishing milling steel
When finishing milling steel, the selection of the optimal insert radius (tip radius Rε) requires comprehensive consideration of factors such as processing quality, tool life, cutting forces and material properties.
Recommended range of inserts radius
General steel (such as 45 steel, S45C, AISI 1045, etc.):
Recommended tool tip radius=0.4 mm∼0.8 mmRε=0.4mm∼0.8mm.
Smaller radius (0.2∼0.4 mm0.2∼0.4mm) is suitable for high-precision detail processing or thin-walled parts.
Larger radius (0.8∼1.2 mm0.8∼1.2mm) is suitable for efficient machining and can improve tool life and chipping resistance.
• High hardness steel (such as hardened steel, die steel H13, D2, etc.):
Recommended =0.2 mm∼0.4 mmRε=0.2mm∼0.4mm to reduce cutting force and avoid edge chipping.