Efficient metal processing tools: turning tools
Whether you are a professional mechanic or a boss, using turning tools for metal processing is the key to improving efficiency and precision.
This article will analyze the selection skills, applicable materials and operation points of metal lathe tools (Lathe Tools) to help you fully realize the potential of lathe tools (Machine Tools for Lathes).
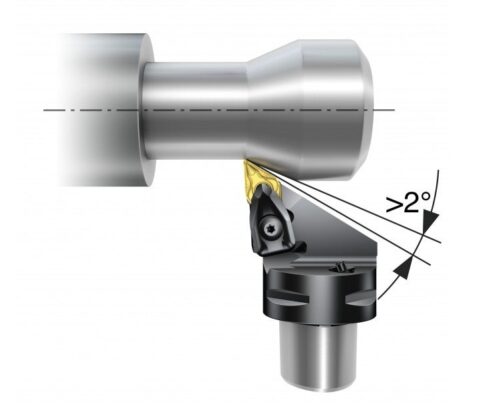
一. Lathe tool recommendation: Precisely match processing requirements
The effect of lathe cutting (Lathe Cutting) depends on the choice of tools. The following are several common high-performance lathe tools:
1. High-speed steel (HSS) lathe tools: suitable for low-speed processing, excellent toughness, can process soft metals such as carbon steel and aluminum alloy.
2. Carbide lathe tools: strong wear resistance, suitable for turning high-hardness materials such as stainless steel and titanium alloy.
3. Ceramic/CBN lathe tools: specially designed for ultra-high-speed cutting, can process extremely hard materials such as hardened steel, and significantly improve efficiency.
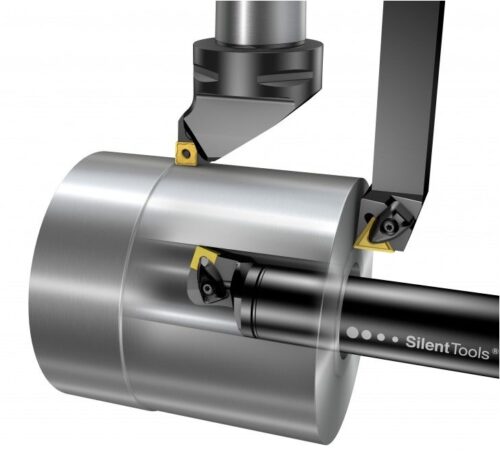
二. Applicable materials analysis: from soft metal to carbide
The performance of turning tools is closely related to the processing materials:
Steel and stainless steel: carbide or coated tools are preferred, and coolant is used to reduce thermal deformation.
Aluminum and aluminum alloys: high-speed steel or diamond tools can prevent material sticking to the tool and ensure surface finish.
Brass/bronze: universal HSS turning tools are sufficient, low cost and easy to maintain.
Titanium alloy: high-rigidity carbide tools are required, and the cutting speed is controlled to prevent overheating.

三. Key points for using turning tools: improve both precision and efficiency
1. Optimize cutting parameters: adjust the speed and feed rate according to the hardness of the material. For example, the speed can be increased when processing aluminum, while the speed needs to be reduced and cooling needs to be increased when cutting stainless steel.
2. Align the tool tip to the center: ensure that the installation height of the turning tool is aligned with the axis of the workpiece to avoid vibration or dimensional deviation.
3. Regularly maintain the blade: grind or replace worn tools in time to prevent the roughness of the machined surface from increasing.
4. Make use of multifunctional toolholders: The modular design of Machine Tools for Lathes supports fast tool change and reduces downtime.
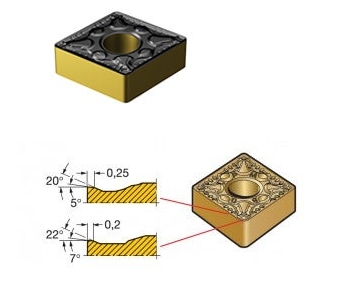
四. Core advantages of turning tools
1. Efficient processing: Carbide and CBN tools can significantly shorten the processing cycle, especially suitable for mass production.
2. High-precision control: Rigid Lathe Tools can achieve micron-level tolerances to meet the needs of precision parts.
3. Outstanding durability: Modern coating technology extends tool life and reduces long-term costs.
4. Multi-functional adaptation: By replacing the blade or cutter head, the same tool can complete a variety of processes such as rough turning, fine turning, and grooving.
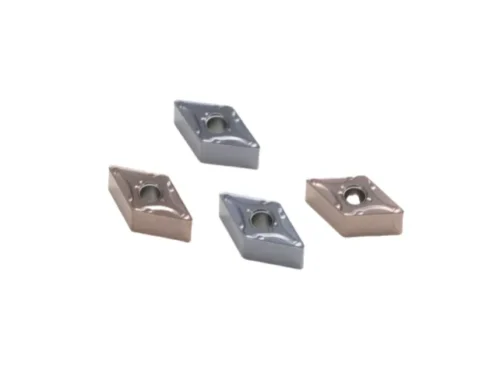
Whether it is the basic operation of lathe cutting or the precision machining of complex parts, it is crucial to choose turning tools reasonably and master their use. It is recommended to match the tool type according to the material characteristics, and pay attention to the cutting parameters and maintenance details to maximize the performance potential of the lathe.